Collaborative Robots in Manufacturing: Trends Shaping the Future of Work
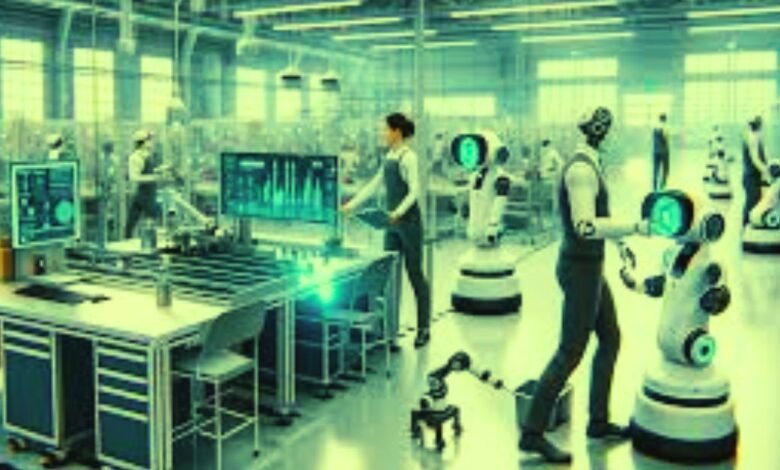
The manufacturing industry has seen significant transformations over the past few decades, driven by advancements in automation, robotics, and artificial intelligence (AI). One of the most exciting developments in recent years is the rise of collaborative robots, or cobots, which are designed to work alongside human workers in a shared workspace. Unlike traditional industrial robots, which operate in isolation or behind safety barriers, cobots are built with advanced sensors, AI capabilities, and safety features to interact with humans safely and efficiently.
As the manufacturing landscape continues to evolve, collaborative robots are playing an increasingly critical role. In this article, we explore the trends shaping the future of work in manufacturing, highlighting how cobots are transforming production processes and creating new opportunities for workers.
1. Increased Adoption of Collaborative Robots
Over the past few years, the adoption of cobots has surged across various manufacturing sectors, including automotive, electronics, and consumer goods. Companies are increasingly recognizing the value of integrating cobots into their operations to enhance productivity, improve quality, and streamline workflows. These robots are particularly valuable in small- and medium-sized enterprises (SMEs) that may not have the resources to invest in traditional automation systems.
Cobots are highly flexible and can be easily reprogrammed for different tasks, which makes them adaptable to the changing needs of a manufacturing line. Unlike traditional robots, which require complex and expensive retooling for new tasks, cobots can be deployed quickly and efficiently, offering significant cost savings and faster return on investment.
2. Enhanced Safety and Human-Robot Collaboration
One of the major benefits of cobots is their ability to work safely alongside human operators. Cobots are designed with built-in safety features, including force sensors, collision detection, and speed control, which ensure that the robots stop or slow down if they come into contact with a human. This feature eliminates the need for physical barriers or safety cages, which are typically required for traditional industrial robots.
This collaborative approach leads to improved workflows, as human workers can focus on tasks that require creativity, decision-making, or dexterity, while cobots handle repetitive, physically demanding, or hazardous tasks. The combination of human skills and robotic precision enhances the overall productivity and efficiency of the manufacturing process.
3. AI and Machine Learning Integration
Artificial intelligence (AI) and machine learning are playing an increasingly important role in the capabilities of cobots. These technologies enable cobots to learn from their environment, adapt to new tasks, and optimize their performance. By integrating AI algorithms, cobots can analyze data from sensors and cameras to make real-time decisions, improving accuracy and speed.
In addition, AI-powered cobots can collaborate more effectively with human workers by understanding and responding to subtle changes in the work environment. This level of adaptability makes cobots even more valuable in dynamic manufacturing environments where conditions can change rapidly.
4. Remote Monitoring and Control
As manufacturing becomes more connected, remote monitoring and control of cobots have become a key trend. With the rise of the Industrial Internet of Things (IIoT), cobots can be monitored and controlled remotely, providing manufacturers with real-time data on robot performance, health, and production outputs.
Remote monitoring allows for predictive maintenance, enabling manufacturers to identify potential issues before they become problems. This helps reduce downtime and ensures continuous, uninterrupted production. Additionally, the ability to control cobots from a distance gives manufacturers the flexibility to manage operations across multiple facilities or production lines.
5. Labor Force Transformation and Upskilling Opportunities
While there are concerns about automation displacing jobs, cobots are helping to create new opportunities for workers. Rather than replacing human workers, cobots are designed to augment their capabilities and enable them to focus on more valuable tasks. This shift is leading to the transformation of the labor force, with a growing emphasis on upskilling and reskilling.
Manufacturers are increasingly investing in training programs that help workers develop the skills needed to operate and maintain collaborative robots. This includes training in robotics programming, AI, machine learning, and data analysis. As a result, workers are gaining new technical skills that improve their employability and career prospects in an increasingly automated industry.
6. Cost Efficiency and Scalability
One of the key reasons for the growing popularity of cobots in manufacturing is their cost-effectiveness. Traditional industrial robots often require significant investments in infrastructure, programming, and maintenance, making them inaccessible to smaller manufacturers. In contrast, cobots are generally more affordable, with lower upfront costs and easier integration into existing production lines.
Cobots also offer scalability, allowing manufacturers to start with a small number of robots and gradually expand their operations as needed. This flexibility enables manufacturers to scale their automation efforts in line with demand, making cobots an attractive option for companies of all sizes.
7. Sustainability and Energy Efficiency
As sustainability becomes a top priority for manufacturers, cobots are contributing to greener, more energy-efficient production processes. These robots are typically designed with energy-efficient components and are capable of operating at optimal speeds without wasting energy. Additionally, cobots can help reduce waste by performing tasks with a high degree of precision, leading to fewer defects and less material waste.
Moreover, by enabling manufacturers to optimize their operations and reduce reliance on human labor for dangerous or repetitive tasks, cobots contribute to safer, more sustainable workplaces.
8. Customization and Flexibility in Production
The rise of cobots is also driving greater customization in manufacturing. Cobots can be quickly reprogrammed or equipped with different tools to perform a wide variety of tasks, from assembly to packaging to quality inspection. This level of flexibility allows manufacturers to produce a wider range of products without the need for extensive reconfiguration or downtime.
As consumer demands continue to shift towards personalized and custom-made products, cobots offer a way to meet these demands without sacrificing efficiency. This trend is particularly relevant in industries like automotive and consumer electronics, where customization is becoming a key differentiator.
Conclusion
Collaborative robots are playing an increasingly important role in the manufacturing industry, driving innovation, enhancing safety, and improving productivity. With advancements in AI, machine learning, and remote monitoring, cobots are becoming smarter, more adaptable, and more cost-effective. These trends are reshaping the future of work in manufacturing, creating new opportunities for workers and transforming production processes for the better.
As manufacturers continue to embrace the benefits of cobots, the collaboration between humans and robots will only deepen, fostering a more efficient, flexible, and sustainable manufacturing ecosystem. With the right investments in technology, training, and infrastructure, the future of manufacturing looks promising, with cobots leading the way.